農業のムダをなくす「豊作計画」とは?
第1部はゲストセッション。まずは特別講師であるトヨタさんのトークからスタートしました。
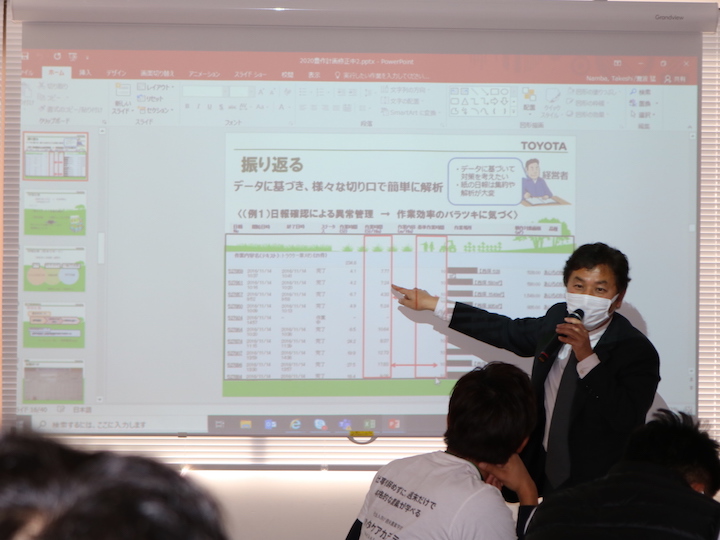
柔らかい語り口ながら、改善に対する真摯(しんし)な姿勢が伝わってくる
トヨタ自動車は言わずと知れた日本有数の自動車メーカーです。トヨタといえば「カイゼン」に代表される「トヨタ生産方式」がよく知られていますが、その肝はムダの徹底排除による原価低減。この生産方式を農業に生かしたのが「豊作計画」というサービスです。現場改善のノウハウを生かして、農家の経営基盤の強化・農業を担う人づくりに貢献することを狙っています。
「皆さん、日頃の農作業でムダだなと感じることはありますか?」
こう尋ねられると多くの参加者が手を上げました。農業においても見直すべきムダがたくさんあることを、皆さん実感しているようです。「豊作計画」ではどのようにムダをなくすことができるのでしょうか。
「豊作計画」は2本の柱からなり、その一つは生産工程管理を実施し、コストを見える化するIT管理ツールです。まずは、圃場(ほじょう)の規模や農作業に携わる人の人数、栽培品目や各作業に要する時間などを、すべてデータベース化して一元管理。その上で、作業計画を立て、実際の作業記録を取り、折々に作業の進捗(しんちょく)を確認し、定期的に振り返りを行うという、いわゆるPDCAをしっかり回すためのツールです。
ただし、どれほど便利なIT管理ツールがあっても、ツールを提供するだけでは大きな効果は望めません。そこで「豊作計画」では、もう1本の柱として改善スタッフを現場に派遣し、徹底的に現場改善に取り組みます。いわば、デジタルとアナログを融合させたところに「豊作計画」のユニークさがあります。
現場改善の基本サポートの一つが「2S(整理整頓)」の徹底です。「整理整頓をすると『正常』な状態が目に見えるようになります。そうすることで初めて『異常』、つまり課題に気づくことができるんです」。そんな例を挙げながら、現場改善の一端を紹介してくれました。
ゲストトークの後は、佐川さんとの対談および質疑応答の時間となりました。
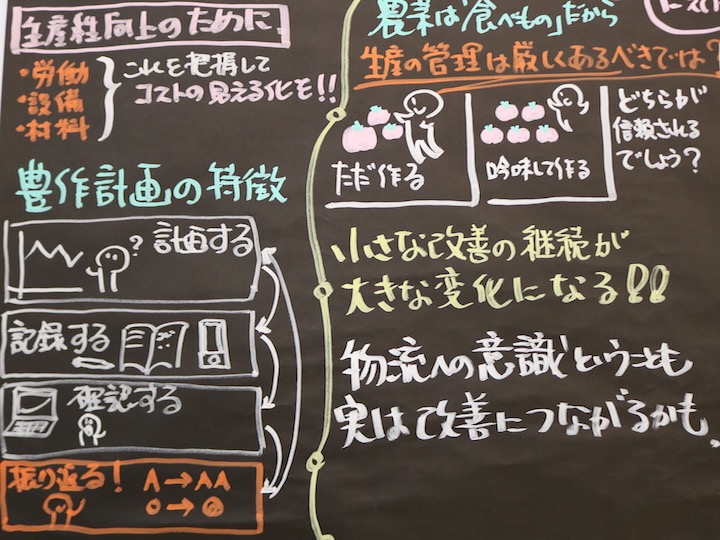
ヨシさんのグラフィックレコード。今回は一部を拡大してご紹介します
対談:農業で実践できるトヨタ式現場改善と課題解決
農業の特殊性や工業との違いはどこか?
佐川:品質管理といったときに、農業と工業・製造業では、やはり求められることが違ってくるのかなと思います。両者を比較して、感じていることをお聞かせください。
トヨタ:クルマにおける品質管理では、不良品を外に出さないことを徹底しています。リコールが起こるようなことになれば信頼が失墜しますから。食べ物を生産している農業では、そこがさらにシビアなのではないでしょうか。その割に、農業には確固とした品質基準がありませんね。本来は、世界の誰が見ても分かるような管理方法が必要だろうと思います。
佐川:すぐに工業並みというわけにはいかないかもしれませんが、農業でも生産者がしっかりとした自分の基準を設け、秀品率を上げていく工夫が必要でしょうね。そうすることで、「オレがウマいと言ってるんだからウマい!」以上の説得力につながると思います。
業務改善を続けるための秘訣(ひけつ)は?
トヨタ:改善活動は現状の否定から始まることがあります。そのため、現場で働く人の反発を招くこともあるでしょう。何より大切なのは、経営者が強い意志を持ち、従業員や仲間と思いを共有することです。経営者であれば、まずは現場を知ることが業務改善の秘訣です。
佐川:現場の意見を尊重するのが大事ですね。阿部梨園での私の経験でも、はじめは自分で100件の改善案を出そうかと思っていました。でも、途中から従業員の方からもアイデアが出るようになり、業務改善がグンと加速したんです。現場の声を吸い上げ続ける仕組みこそが、本質的には大切だと感じます。
農業の課題は? 希望は?
トヨタ:農業では天候をコントロールできないように、トヨタは為替変動の影響を避けられません。そうした外部要因に振り回されないようにすることが、農業でも工業でも共通の課題です。常日頃から対策を考え、いざというときの「復興プラン」を立てておくことです。例えばトヨタでは、為替の動きが悪くなると、ムダな電気を消すといった小さなことから経費削減に努めることが習慣づけられています。
佐川:コスト削減をあきらめてはいけませんね。少しでも原価率を下げることで、ほかに利益を配分することもできますし、やはりコスト削減は大きなテーマの一つだとあらためて感じます。
トヨタ:農業にはまだまだ変革の余地があり、あらゆるムダを排していくことで、大きなチャンスがあると見ています。というのも、今の食料自給率(カロリーベース)は40%にも届きませんよね。ある意味で、国内市場が頭打ちの自動車業界より、はるかに伸びしろが大きいと言えるでしょう。
参加者との質疑応答から
──改善より目先の仕事に忙殺されてしまいがちです。農家の方をサポートする立場から、改善を習慣づけるために、どういうアプローチを取ればいいのでしょうか。
トヨタ:ぜひお勧めしたいのは、定期的な振り返りを行うことです。週に30分でいいので、皆さんでミーティングをしてください。業務の一環として、しっかり振り返りの時間を取ることが必要不可欠です。
佐川:少量多品目の改善の難しさにもつながる話ですね。少量多品目の栽培では、一つ一つの品目に対してPDCAの学習サイクルを回す機会が少ない。振り返りがなかなかできないため、改善が進みづらいんです。私はたとえ年に一度しかしない作業についても、作業後すぐに、翌年のために気づきをまとめておくことにしています。
参加者の熱気に包まれた中、対談と質疑の時間は過ぎ、第1部は終了になりました。
課題解決をテーマにしたワークショップ
第2部は、課題解決をテーマにしたワークショップを行いました。まずは一人一人、日頃の業務を振り返りながら、トヨタ式の「課題整理シート」に現状の問題やその要因、対策や目標などを書き込みます。各テーブルにはトヨタの方々がつき、参加者の皆さんの真の課題を掘り下げるサポートをしてくれました。続いて、グループごとのディスカッションを通して、課題整理を深めていきました。このワークでの気づきをそれぞれの現場に持ち帰り、実際の改善につなげていただければと思います。
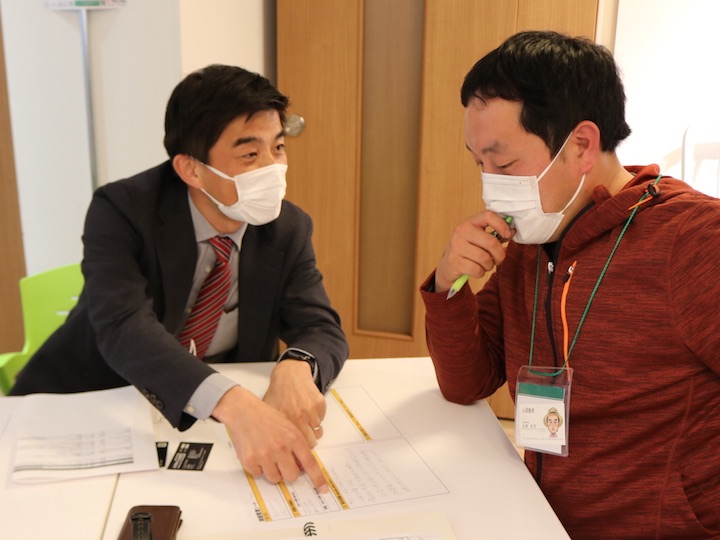
ワークショップでは「豊作計画」のサポートを模擬体験
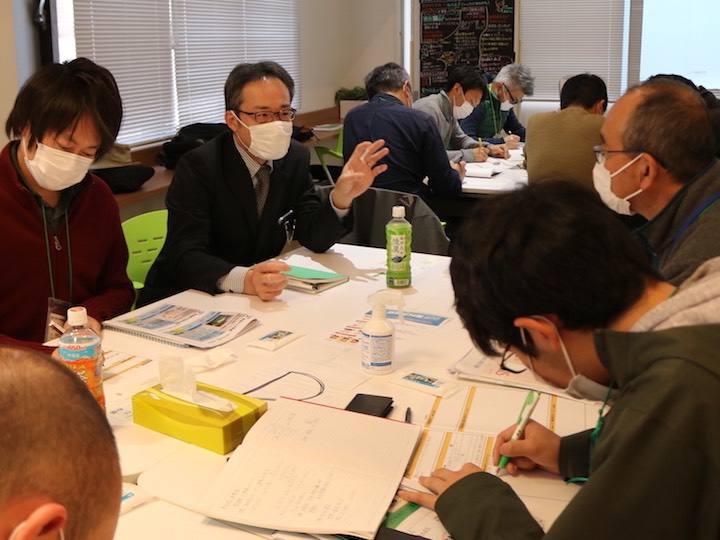
「なぜ?」を繰り返し、真の課題を掘り下げるのがトヨタ式