露地栽培に見劣りしない大きさのレタス
東京都江東区にある東京ビッグサイトで2019年8月下旬に開かれた食品関連の展示商談会。抹茶を使ったさまざまな飲料や米国の牛肉、国産のパスタ、熊本の馬刺し、さらにラーメンスープや和風だしなど、膨大な数の魅力的な展示を脇に見ながら、真っ先に向かったのが、植物工場を運営するMIRAIのブースだった。社長の野澤永光(のざわ・ながてる)さんから「ようやく工場を改造できました。その成果を、展示会でお見せできます」と誘われていたからだ。
そこにあったのは、工場製としてはそれまで見たことのない大きさのレタスだった。
現在、工場で作られている野菜は結球しないリーフレタスがほとんどで、重さは80グラムが中心。スーパーなどで販売されており、指先でつまんでひょいと持ち上げることができる大きさだ。一回で食べきるにはちょうどいいが、露地で育てたレタスと比べると、どうしても小さく感じてしまう。
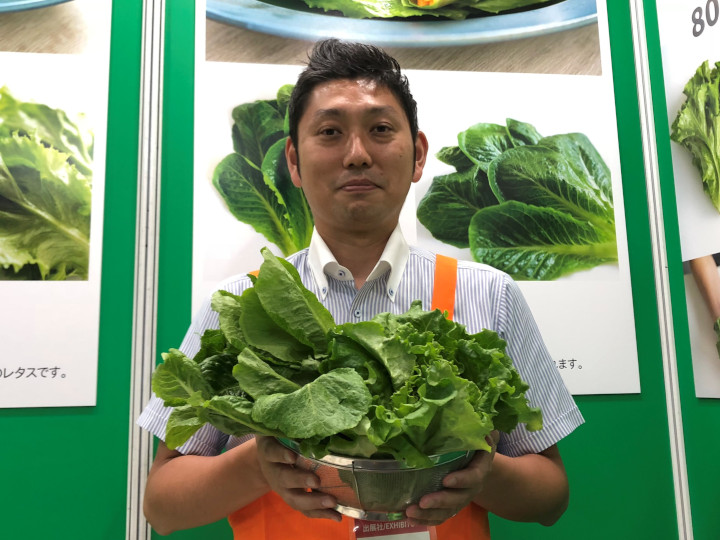
「ようやく前進できる」と話すMIRAI社長の野澤永光さん(東京ビッグサイトの展示会にて)
これに対し、野澤さんがそのとき見せてくれたレタスは、重さがこれまでの3倍以上の250グラム。手にとってみると、「ずしり」とまではいかないが、確かに重さを感じることができた。手のひらに乗るサイズの既存の工場レタスと違い、露地モノと比べても見劣りしない大きさで、葉っぱも厚い。
MIRAIは千葉県柏市と宮城県多賀城市の2カ所で植物工場を運営している。そのうち柏市の工場の設備の一部を、6月から8月にかけて改造した。ポイントの一つは、レタスを育てる栽培棚の段数を、11段から7段に減らしたこと。高さは4.5メートルのまま変えなかったので、上下の棚同士の間隔が広がった。その分、栽培空間に余裕ができたわけだが、それだけでレタスが大きく育つわけではない。
もっと重要なのは、栽培方法だ。野澤さんによると、「発光ダイオード(LED)照明の当て方や、棚を流れる水の速さ、棚と棚の間の空気の流れ方を変えた」。